Oliver Arend
Administrator
Administrator
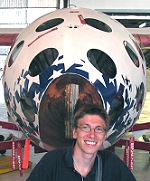
Registriert seit: Aug 2000
Wohnort: Great Falls, VA, USA
Verein: RMV/Solaris/AGM/TRA L1/TCV/MDRA/NOVAAR
Beiträge: 8333
Status: Offline
|
So, damit Ihr nicht denkt, die Rakete entsteht wieder nur im Rechner, wollte ich Euch heute mal den aktuellen Stand meiner V2 aus Metall präsentieren. Hier zunächst ein Überblick: Die vier langen Teile sind T-Profile, die die Außenkontur des unteren Rumpfteils bilden und an denen Motorführungsschienen befestigt sind. Hier so eine Motorhalterung im Detail: Die Verbindung wird mit Parallelogramm-förmigen Blechen hergestellt, die außerdem mit einem Winkel versteift wurden. Auf der Innenseite des T-Profils ist außerdem ein Stück Kunststoff angebracht, um das Casing vor der Eloxalschicht (und damit evtl. Kratzern) zu schützen. Der Kunststoff ist mit Senkkopfnieten befestigt: Außerdem ist oben in der Mitte eine Aluplatte zu sehen. Diese bildet den Boden der Fallschirmkammer. In die Mitte kommt noch eine Ringschraube zur Aufnahme der Shock Cord. Um die auftretenden Kräfte besser in die Raketenstruktur abführen zu können, wurde die Platte mit vier Vierkant-Stücken versteift. Die Schlitze an den Seiten sind für die "Stämme" der T-Profile. Am Umfang werden noch gebogene Winkel vernietet, um der Rakete auch im Querschnitt ihre Form zu geben. Die gebogenen Winkel sind auf dem folgenden Foto zu sehen. Diese sind so geformt, dass die Rakete dort einen Außendurchmesser von 180 mm hat. Die grauen "Tannenbäumchen" auf der Innenseite stammen vom Stauchen, da sich dort Risse im Eloxal bilden -- nicht-eloxierte Profile gab es im Baumarkt leider keine (mehr). Natürlich gibt es davon noch mehr für die anderen Durchmesser im Bereich des Hecks und in der Spitze. Nun noch zu den technischen Daten: Länge 1575 mm Durchmesser 180 mm Spannweite 420 mm Leermasse ca. 4-7 kg (hängt ganz stark von der Stärke der Beplankung ab, im Moment plane ich mit 0,5 mm) Motormount 38 mm Da ich mir beim Gewicht noch nicht sicher bin (Gewicht in der Spitze?!), kann die Motorhalterung prinzipiell jeden 38 mm-Motor aufnehmen. Damit dürften 4-7 kg gut abgedeckt sein, und mit einem Blue Thunder und dem entsprechenden Tritt in den Hintern sollte man auch eine V2 stabil bekommen. Fragen, Kritik und Anregungen dürfen gerne hier im Thread gestellt werden. Oliver
Geändert von Oliver Arend am 07. März 2010 um 22:36
|
Zaphod
Epoxy-Meister

Registriert seit: Feb 2007
Wohnort: Alsbach-Hähnlein
Verein: TU-Darmstadt
Beiträge: 425
Status: Offline
|
Sieht schon sehr gut aus. Schon ne Idee, wie Du die Beplankung in Form bringen willst?
Gruß, Marco
|
Oliver Arend
Administrator
Administrator
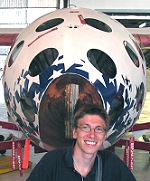
Registriert seit: Aug 2000
Wohnort: Great Falls, VA, USA
Verein: RMV/Solaris/AGM/TRA L1/TCV/MDRA/NOVAAR
Beiträge: 8333
Status: Offline
|
Jein ... ich befürchte, es wird etwas mit Pressen oder Ziehen zu tun haben. Ob das bei 0,5 mm Weichalu aber noch so gut klappt, weiß ich nicht. Einer unserer Mechaniker hat mir angeboten, mal bei seinem alten Ausbildungsbetrieb nachzufragen, ob man sich mit einem Hartholzpositiv und ein paar Blechen mal in deren Gummikofferpresse (Gummiblock wird von oben auf die Form gepresst, man braucht also keine zwei Formen) stellen kann. Natürlich kann man sich auch überlegen, ob man mit einem Wagenheber o.ä. so eine Presse selbst baut, aber das wäre dann noch ein anderes Winterprojekt ...
Den Kern sollte ich in Stuttgart in der Akamodell CNC-fräsen können.
Oliver
|
Neil
99.9% harmless nerd
Administrator

Registriert seit: Aug 2000
Wohnort: Delft
Verein: SOLARIS
Beiträge: 7776
Status: Offline
|
Hi,
machst du da Formen für die Originalblechstücke, oder planst du eine Form über die gesamte Länge?
Gruß
Neil
Die Erde ist eine Scheibe. Egal in welche Richtung sich die Menschheit bewegt, sie geht immer auf einen Abgrund zu.
|
osmadie
SP-Schnüffler
Supervisor

Registriert seit: Feb 2006
Wohnort: Rhein-Pfalz-Kreis
Verein: Solaris-RMB e.V.
Beiträge: 515
Status: Offline
|
Hi Oliver!
Das Projekt macht wirklich was her. Das ist echt klasse!
Wenn es nur um's Pressen geht, könnte ich Dir vielleicht auch aushelfen. In meinem Keller steht eine (noch nicht ganz fertige) selfmade 6-Tonnen-Presse. Nur mit einem Gummi-Klotz kann ich nicht dienen, aber vielleicht tun es auch eine Menge alte Stoff-Lappen, die man oben drauf knüllt und am seitlichen wegquetschen hindert...
Wie groß sollen die einzelnen Planken denn sein?
Gruß Oliver
Der erste Schluck aus dem Becher der Wissenschaft führt zum Atheismus, aber auf dem Grund des Bechers wartet Gott. Werner Heisenberg
|
Zaphod
Epoxy-Meister

Registriert seit: Feb 2007
Wohnort: Alsbach-Hähnlein
Verein: TU-Darmstadt
Beiträge: 425
Status: Offline
|
Könntest ja aus mehreren Alu-Folienlagen nen Sandwich herstellen  Aber 0,5er Blech bekommst Du mit kleinen Kräften schon gut geformt.
|
Oliver Arend
Administrator
Administrator
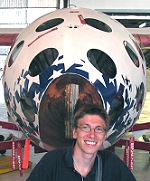
Registriert seit: Aug 2000
Wohnort: Great Falls, VA, USA
Verein: RMV/Solaris/AGM/TRA L1/TCV/MDRA/NOVAAR
Beiträge: 8333
Status: Offline
|
Ich wollte eine Form für einen 90°-Abschnitt der Spitze und eine für 90° des Hecks machen. Damit bleiben Verformung und Größe der Form überschaubar. Der zylindrische Teil in der Mitte wird einfach so vernietet, dass er von selbst zylindrisch wird. Die Blechrohlinge dürften so um die 650x200 groß sein (müssen). Für das Heck kürzer. Wie das Verfahren selbst genau aussieht, weiß ich nicht, aber man braucht offenbar etwas, was sich der Form möglichst genau und vollständig anpassen kann. Eine entsprechende Menge Silikon-Gießmasse von R&G ist ja unbezahlbar. Ich hatte auch noch überlegt, das Blech in einen Rahmen einzuspannen, und diesen dann über den Kern tiefzuziehen. Meint Ihr das könnte Klappen? Oliver
Geändert von Oliver Arend am 08. März 2010 um 14:22
|
Zaphod
Epoxy-Meister

Registriert seit: Feb 2007
Wohnort: Alsbach-Hähnlein
Verein: TU-Darmstadt
Beiträge: 425
Status: Offline
|
Ums dengeln und drücken wirst Du bei der Größe nicht herumkommen
Geändert von Zaphod am 08. März 2010 um 15:03
|
Neil
99.9% harmless nerd
Administrator

Registriert seit: Aug 2000
Wohnort: Delft
Verein: SOLARIS
Beiträge: 7776
Status: Offline
|
Hi, um meinen ehemaligen Prof. für metallische Werkstoffe glücklich zu machen, schlage ich das Sprengumformen vor. Das würde deiner Idee des Tiefziehens am nächsten kommen.  Gruß Neil
Die Erde ist eine Scheibe. Egal in welche Richtung sich die Menschheit bewegt, sie geht immer auf einen Abgrund zu.
|
osmadie
SP-Schnüffler
Supervisor

Registriert seit: Feb 2006
Wohnort: Rhein-Pfalz-Kreis
Verein: Solaris-RMB e.V.
Beiträge: 515
Status: Offline
|
Ich habe ja kaum Erfahrung mit Blechen biegen... Müsste die Biegeform nicht sogar eine kleine Überdehnung bewirken, damit beim entspannen die Form etwas zurückfedern kann und dann erst die (möglichst) optimale Form zum vernieten bekommt? Oder ist eine kleine Vorspannung beim Vernieten egal?
Gruß Oliver
Der erste Schluck aus dem Becher der Wissenschaft führt zum Atheismus, aber auf dem Grund des Bechers wartet Gott. Werner Heisenberg
|
|