Ich hatte ja während meines Praktikums Zugriff auf reichlich Glasfaser, Harz, Werkzeuge und anderes Material und außerdem nach Feierabend und am Wochenende wenig zu tun... Ich wollte ursprünglich eine ganze Rakete nach dem Prinzip Stringer-Spanten aufbauen, dafür hat die Zeit dann aber doch nicht mehr gereicht.
Die Idee ist, kein einfaches hohlzylindrisches Körperrohr zu verwenden, da ein solches knickanfällig ist. Stattdessen werden Längsversteifungen (Stringer) und Querversteifungen (Spanten) eingebaut, und die Wandstärke dafür verringert. In der Theorie ergibt dies eine leicht verringerte Festigkeit gegenüber Biegemomenten, bei gleichem Gewicht und gleicher Zugfestigkeit. In der Praxis vermeidet es jedoch Knickung, das bei Kompression (und entspr. auch Biegung) auftreten kann.
Aus Mangel an einer Negativform habe ich das Rohr auf einem Positivkern aufgebaut. Dazu zuerst ein möglichst rundes Alurohr genommen, und dieses einmal mit Mylarklebeband umwickelt. Spiralförmig, und so dass es wieder Lücken noch Überlappungen gab. Das ganze wurde dann gewachst.
Um diese Lage Mylar herum wurde noch einmal spiralförmig eine Lage Mylarband gewickelt, diesmal jedoch mit der Klebeseite nach außen. So entstand die erste Trennebene. Auf dieser Lage Mylarband wurde dann ein Negativ der inneren Struktur des Körperrohrs aufgebaut. Dazu benötigte ich flexibles, dünnes (rund 2 mm) aber halbwegs druckfestes Material. Depron habe ich nich gefunden, also musste ich Styrodurblöcke in dünne Scheibchen schneiden. Aus diesen habe ich dann mit einer Rasierklinge kleine Platten ausgestanzt.
Hier eine Ansammlung von acht Platten, die auf 100 mm Länge für den gesamten Umfang ausreichen.
Diese Platten wurden dann gleichmäßig auf dem Körperrohr verteilt, mit kleinen Zwischenräumen, in denen später die Stringer und Spanten entstehen würden. Man erkennt sehr schon die Längs- und Querverläufe. Das ganze Rohr wird 700 mm lang und hat einen Durchmesser von rund 85 mm.
Natürlich kann man da noch nicht drauflaminieren, denn das Styrodur soll ja später nicht Bestandteil des Körperrohrs werden. Also noch einmal eine Lage Mylarband drauf, das klappte natürlich nicht mehr ganz so schön mit den ganzen Ecken und Kanten.
Nachdem die Form so vorbereitet war (wachsen lohnte sich hier nicht mehr, das Material wird ja von innen einfach abgezogen), ging es nun endlich an die Herstellung der Struktur. Wir benutzten für unsere großen Teile 900 g/m²-Gewebe, aus dem ich einfach einzelne Fäden herausgezogen und als Roving verwendet habe. Pro Stringer und Spant wurden jeweils überlagernd drei solcher Rovings verwendet. Das bedeutet natürlich einen gewissen Dickezuwachs an den Kreuzungen.
Ich hätte sie einzeln mit Harz tränken sollen, denn drei Rovings auf einmal (entspr. einer Gewebestärke von 2700 g/m²!) lassen sich kaum noch gescheit tränken, außer mit _viel_ Harz. Da nun die Längs- und Querfestigkeit bereits stand wollte ich Verdrehungen und Verschiebungen vermeiden und habe als Oberfläche eine Lage bidirektionales Gewebe in 45°-Orientierung auflaminiert.
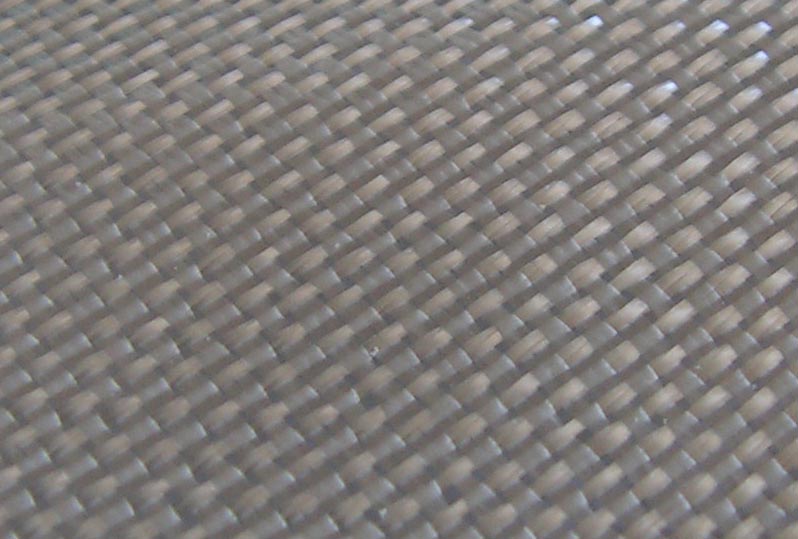
Das ganze erhielt zum Abschluss für eine gut bearbeitbare Oberfläche (und zum Entfernen von Harznasen, wie sich später herausstellen sollte) eine Lage Abreißgewebe, das hier an den schwarzen eingewobenen Fäden erkennbar ist. Leider auch erkennbar sind die vielen Luftblasen, die sich nicht vermeiden ließen.
Hier das fertige Rohr, innen konnte ich das meiste Klebeband entfernen, das Styrodur hatte ich mit Aceton ausgespült. Die Trennung vom eigentlichen Kern gelang mit acht starken Händen recht einfach (es geht offenbar nix über Achims Luftkissen-Methode).
Die beiden Enden hatte ich plangeschliffen, so dass das Rohr direkt hätte weiterverwendet werden können, zumal der Innen-innen-Durchmesser durch den Kern sehr genau definiert war (im Gegensatz zum Außendurchmesser). Hier ein Blick nach innen, wo man die Stringer und Spanten sehr schön erkennt.
Ich habe das Rohr leider nicht mit nach Deutschlánd/Frankreich nehmen können (zuviel totes Volumen), aber wenigstens habe ich dabei einiges gelernt.
Das Rohr wog fertig, wie oben auf dem Foto, bei einer Länge von rund 700 mm und einem Außendurchmesser von rund 85 mm, etwa 230 g. Das ist nicht ganz wenig, aber auch nicht sehr viel. Das 3-Zoll-Rohr in Phenolic von PML wiegt bei geringerem Durchmesser und gleicher Länge 280 g. Ich konnte keine genauen Festigkeitsversuche durchführen, die bessere Knickfestigkeit konnte man jedoch ganz einfach erfühlen. Alles in allem würde ich diesem Rohr ohne weiteres einen H- oder I-Motor zutrauen.
Ich bin jedoch bei der Herstellung auf Probleme gestoßen, und vor allem hat mich das Ergebnis nicht besonders befriedigt. Einmal ist die Herstellung der Form sehr ungenau und sehr aufwändig. Und sie ist nur einmal verwendbar. Die Arbeitsweise in Positivform ergibt eine sehr schlechte Oberfläche, sowohl Rauigkeit als auch Rundheit des Körperrohrs insgesamt. Als Lösung bietet sich hierfür eine zweiteilige Negativform an, in die man zuerst die Außenlage einlaminiert, und dann die einzelnen Stringer und Spanten nur noch einlegen braucht. Allerdings würde so die Genauigkeit der inneren Struktur etwas leiden. Und schlangenförmige Stringer bringen festigkeitsmäßig wenig.
Ebenso war ich mit dem Gewicht nicht zufrieden. Die drei Rovings waren wahrscheinlich etwas Overkill. Es böte sich hier wohl an, insgesamt mit niedrigeren Flächengewichten für die Gewebe zu arbeiten, sowie Styrodurprofile zu verwenden, um Volumen für die Stringer und Spanten aufzubauen. Dieses würde auch die Genauigkeit in der Fertigung steigern.
Insgesamt war der Versuch jedoch sehr lehr- und aufschlussreich. Der Gewinn an Festigkeit mit einer solchen Konstruktion, die über größere Wandstärken nur mit großer Gewichtszunahme zu erreichen ist, ist beachtlich. Evtl. habe ich einmal die Möglichkeit, die Festigkeit von Rohren verschiedener Art etwas wissenschaftlicher zu untersuchen (Zug-, Kompressions- und Biegeversuch(e)).
Oliver
Geändert von Oliver Arend am 26. Oktober 2005 um 14:49